Where reducing waste improved quality
Where reducing waste improved quality
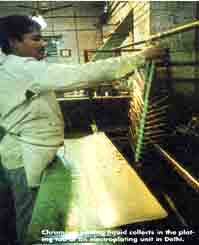
ELECTROPLATING units use highly toxic compounds to produce the shiny "chrome-plated" parts that comprise various gadgets. Nearly all electroplating is done in the unorganised sector by units operating out of small sheds in residential or industrial areas. They do job work for large units, assembling radios and TVs, and in the process, take on the units' dirty jobs.
One item that can be recycled to minimise waste is chromium salt, which is used as a medium in electroplating, and M C Engineering in Okhla in Delhi has shown how. By investing just Rs 5,000, the company has eliminated totally waste of chromium salts.
Explains plant foreman Swaroop Singh, "The items to be plated are normally dipped in a bath of chromium sulphate. When they are taken out, they are rinsed immediately in running water." This led to considerable toxic discharges from the factory. But now, "the plated items are put on hangers above the plating tub to let the excess plating liquid drain into the tub."
Thereafter, another worker takes the items to a neighbouring tub, containing stagnant water, for another dip after which the items are finally rinsed. The waste water that finally emerges from the plant is well within the limits for chromium prescribed by the pollution control authorities. Eventually, the concentration of chromium sulphate in the first rinse tub increases to a level where it can be used for electroplating.
M C Engineering proprietor O N Sharma reels off an impressive list of figures for the savings effected by the measures. His company is a small-scale unit, which employs 25 people and produces 30,000 pieces of equipment a day. The investment on the tub and steel frame was recouped in just 15 days, and the unit made annual savings of Rs 60,000, essentially on account of the reduced demand for chromium sulphate. An added bonus was the drop in the rejection rate of items from 2 per cent to 1 per cent.